Prevention of electrostatic in paint production 2
- Share
- publisher
- ALPTEC
- Issue Time
- Aug 22,2020
Summary
There are the following situations in places prone to static electricity fire accidents during the paint production process.
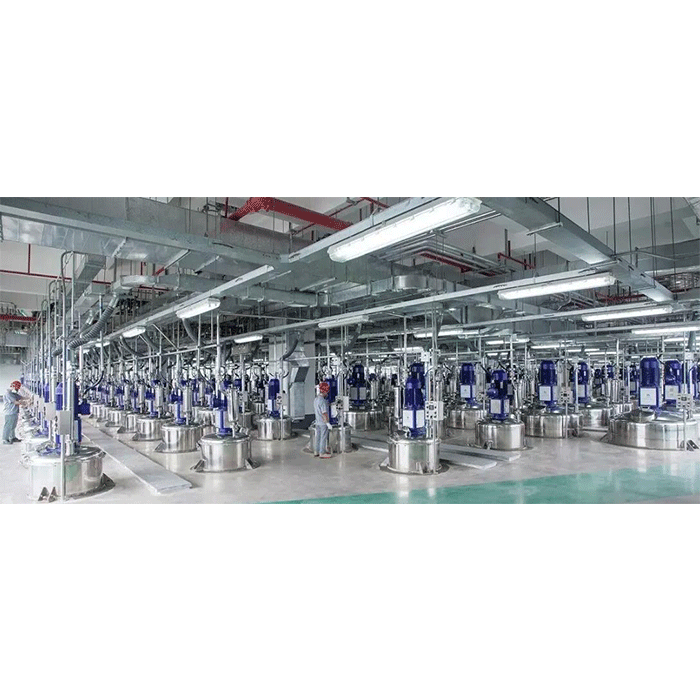
In the paint production
process, the biggest hazards caused by static electricity are explosions and
fires. Although the amount of static electricity is not large, because of its
high voltage, it is prone to discharge and electrostatic sparks. Therefore, in
workplaces with flammable liquids, static sparks may cause fires;
In places with explosive gas
mixtures or explosive fiber mixtures, an explosion may be caused by static
sparks.
There are the following
situations in places prone to static electricity fire accidents during the
paint production process.
1.When
using pipes to transport solvents and resins with resistivity in 1011-1015 ohm·cm,
especially when using plastic pipes such as polyethylene, static electricity is
more likely to occur. Experiments show that when using polyethylene plastic
pipe to transport toluene, the static voltage can be measured as high as 25,000
volts.
For
example, a paint factory used a plastic tube to pump toluene from a 53-gallon
iron bucket to a storage tank. The first bucket was pumped smoothly. Then,
about two-thirds of the second bucket was pumped, an explosion occurred and
caused a fire. An operator died. The reason is that when the plastic pipe
transports toluene, it rubs with toluene to generate static electricity, and
the discharge spark ignites the toluene vapor and causes a fire.
2.When
pouring a solvent with a resistivity of 107-1011 ohm·cm,
if the solvent has a strong impact with the container, or the scouring splash
will generate static electricity.
For
example, a paint factory uses an oil tank truck to load and unload the fuel oil
for the boiler. The tank truck stops at the entrance of the oil storage tank,
inserts the oil drain hose into the oil inlet of the oil storage tank, opens
the cut-off door and the upper cover of the tank truck tank, and starts
unloading. After working for about a minute, there was a sudden explosion with
a loud noise, which caused a fire. The reason is that the position of the oil
pipeline is too high, as much as 3 meters from the oil surface, and the oil
directly impacts the liquid surface in the tank to generate static electricity.
The tank car body, the tank and the oil discharge hose and other oil unloading
facilities have no conductive grounding device, and the static charge cannot
release, generated electrostatic discharge sparks causing oil vapor
deflagration.
3.Static electricity may be generated during the resin
dilution process and the mixing process of paint mixing. Also in the filtration
process of solvents, resins and varnishes, static electricity will also be
generated due to the friction between the material, the container and the
filter.
A paint factory used a 20-mesh wire mesh nailed on a wooden frame as a filter, and the iron red paint slurry was pumped by a gear pump through the filter into a storage tank, and a fire accident occurred. The reason is that the wooden frame barbed wire filter rests on the storage tank and is in an insulated state. The static electricity generated by the friction between the iron red paint paste (phenol alcohol paint paste) and the filter screen cannot leak and gradually accumulates. Finally, the discharge spark causes combustion.
4.When the resin is smelted, sampling with a metal sampler can also generate static electricity.
For example, when a paint factory is refining phenolic
resin, a small iron spoon is used as a sampler to take samples. Burning
occurred when the iron spoon left the resin surface after sampling. The reason
is that when the sampler quickly leaves the resin, it rubs against the resin to
generate electrostatic discharge sparks, which ignite the solvent vapor in the
pot and burn.
5.When organic powders such as phthalic anhydride,
pentaerythritol and rosin are fed, static electricity will be generated when
the powder rubs and collides with the container wall or other appliances.
A paint factory injected 20 kg of caustic soda with water
into the reactor to clean the aluminum powder defloating liquid on the walls of
the kettle. When the stirrer was turned on for about half a minute, the
operator heard a violent reaction sound like a pot boiling in the kettle, and
immediately stopped stirring. However, the aluminum powder slurry and lye were
sprayed violently from the feeding port of the reactor, and went straight to
the roof. After a few seconds, an explosion and burning occurred. The reason is
that the caustic soda reacts violently with the aluminum powder to generate
hydrogen gas, and strong friction occurs when it is sprayed from the mouth of
the kettle, generating high-potential static electricity, which causes an
explosion after discharge.
The hazards of static electricity to paint production, in
addition to causing explosions and fire accidents, can also cause electric
shock injuries.